钢结构构件之间的连接多采用焊接连接,作为钢结构应用最广泛的一个基本连接方式,也是保证钢结构建筑质量中的一个重要环节。钢结构发展的同时,也在朝着大型化、复杂化、高容量、高参数方向发展,其工作条件也越来越苛刻,由焊接问题所造成的质量事故也越来越频繁,危害性也越来越严重。故而,对采用焊接连接的钢结构,提高和保证其焊接质量已成为当前焊接施工中的主要问题。
焊缝质量等级设计
GB50017-2017《钢结构设计标准》规范规定:焊缝应根据结构的重要性、荷载特性、焊缝形式、工作环境以及应力状态等情况,按下述原则分别选用不同的质量等级:
- 在需要进行疲劳计算的构件中,凡对接焊缝均应焊透,其质量等级为:
- 作用力垂直于焊缝长度方向的横向对接焊缝或T型对接与角接组合焊缝,受拉时为一级,受压时应为二级;
- 作用力平行于焊缝长度方向的纵向对接焊缝应为二级。
- 不需要计算疲劳的构件中,凡要求与母材等强的对接焊缝应予焊透,其质量接等级当受拉时应不低于二级,受压时宜为二级。
- 重级工作制和起重量Q≥50t的中级工作制吊车梁的腹板与上翼缘之间以及吊车桁架上弦杆与节点之间的T形接头焊缝均要求焊透,焊缝形式一般为对接与角接组合焊缝,其质量等级不应低于二级。
- 不要求焊透的T形接头采用的角焊缝或部分焊透的对接焊缝,以及搭接连接采用的角焊缝,其质量等级为:
- 对直接承受动力荷载且需要验算疲劳的结构和吊车起重量等于或大于50t的中级工作制吊车梁,焊缝的外观质量标准应符合二级;
- 对其它结构,焊缝的外观质量标准可为三级。
焊缝的检查验收
《钢结构工程施工质量验收规范》(GB50205-2001)规定焊缝按其检验方法和质量要求分为一级、二级和三级。设计要求全焊透的一级、二级焊缝则除外观检查外,还要求用超声波探伤进行内部缺陷的检验,超声波探伤不能对缺陷作出判断时,应采用射线探伤检验,并应符合国家相应质量标准的要求。一级焊缝超声波和射线探伤的比例均为100%,二级焊缝超声波探伤和射线探伤的比例均为20%且均不小于200mm。当焊缝长度小于200mm时,应对整条焊缝探伤。三级焊缝只要求对全部焊缝作外观检查。
焊缝表面不得有裂纹、焊瘤等缺陷。一级、二级焊缝不得有表面气孔、夹渣、 弧坑裂纹、电弧擦伤等缺陷。且一级焊缝不得有咬边、未焊满、根部收缩等缺陷。
一级、二级焊缝的质量等级及缺陷分级应符合下表的规定。
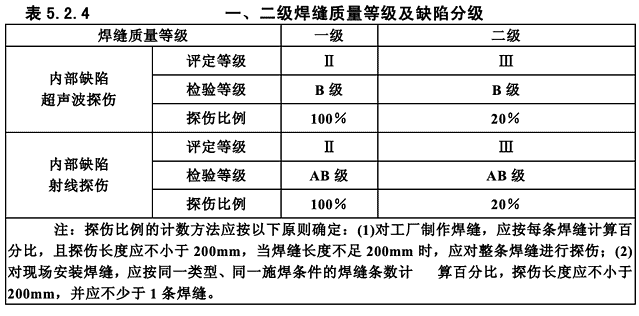
二级、三级焊缝外观质量检查时,焊缝感观应达到:外形均匀、成型较好,焊道与焊道、焊道与基本金属间过 渡较平滑,焊渣和飞溅物基本清除干净。质量标准应符合下表规定。三级对接焊缝应按二级焊缝标准进行外观质量检验。
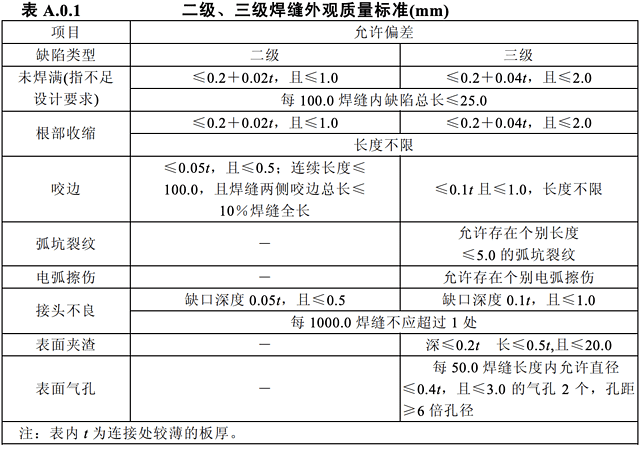
焊缝缺陷
焊缝缺陷指焊接过程中产生于焊缝金属或附近热影响区钢材表面或内部的缺陷。常见的缺陷有裂纹、焊瘤、烧穿、弧坑、气孔、夹渣、咬边、未熔合、未焊透等;以及焊缝尺寸不符合要求、焊缝成形不良等。裂纹是焊缝连接中最危险的缺陷。产生裂纹的原因很多,如钢材的化学成分不当;焊接工艺条件(如电流、电压、焊速、施焊次序等)选择不合适;焊件表面油污未清除干净等。

裂纹
裂纹端部形状尖锐,应力集中严重,对承受交变和冲击载荷、静拉力影响较大,是焊接过程中最危险的缺陷。按其产生的原因通常有热裂纹和冷裂纹之分。
冷裂纹指在200℃以下产生的裂纹,产生冷裂纹的主要原因是焊接结构设计不合理、焊缝布置不当、焊接工艺措施不合理,如焊前未预热、焊后冷却快等。
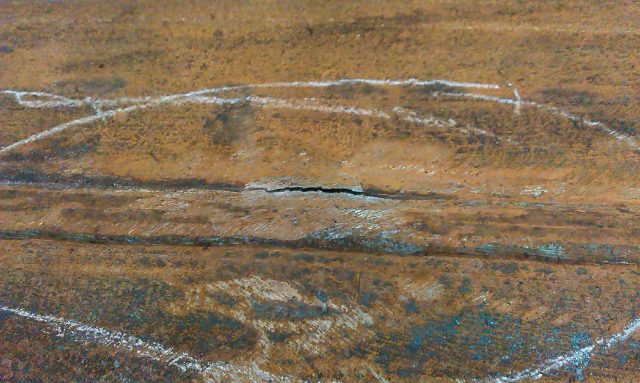
热裂纹指在300℃以上产生的裂纹,产生热裂纹的主要原因是母材抗裂性能差、焊接材料质量不好、焊接工艺参数选择不当、焊接内应力过大等。
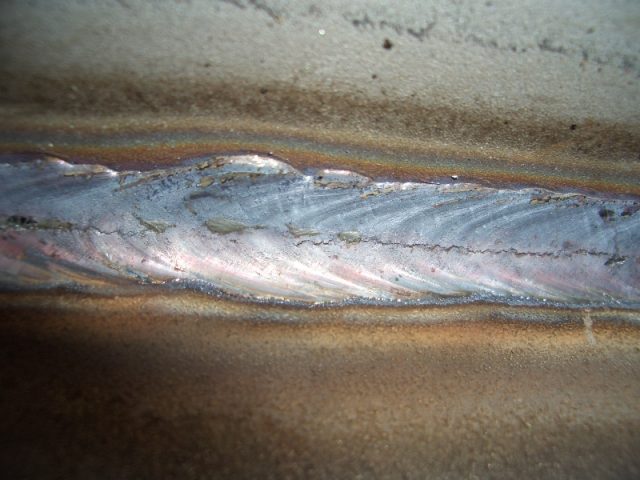
处理办法:在裂纹两端钻止裂孔或铲除裂纹处的焊缝金属,进行补焊。
防治措施:
- 注意焊接接头坡口形式,消除焊缝不均匀受热和冷却因热应力而产生的裂纹。如不同厚度的钢板对焊时,对厚钢板就要做削薄处理。
- 选用材料一定要符合设计图样的要求,严格控制氢的来源,焊条使用前应进行烘干,并认真清理坡口的油污、水分等杂质。
- 焊接中,选择合理的焊接参数,使输入热量控制在800~3000℃的冷却温度之间,以改善焊缝及热影响区的组织状态。
- 在焊接环境温度较低、材料较薄,除提高操作环境温度外,还应在焊前预热。焊接结束要设法保温缓冷和焊后热处理,以消除焊缝残余应力在冷却过程中产生的延迟性裂纹。
孔穴
通常分为气孔和孔坑缩孔两种。产生气孔的主要原因是焊条药皮损坏严重、焊条和焊剂未烘烤、母材有油污或锈和氧化物、焊接电流过小、弧长过长,焊接速度太快等。产生弧坑缩孔的主要原因是焊接电流太大且焊接速度太快、熄弧太快,未反复向熄弧处补充填充金属等。
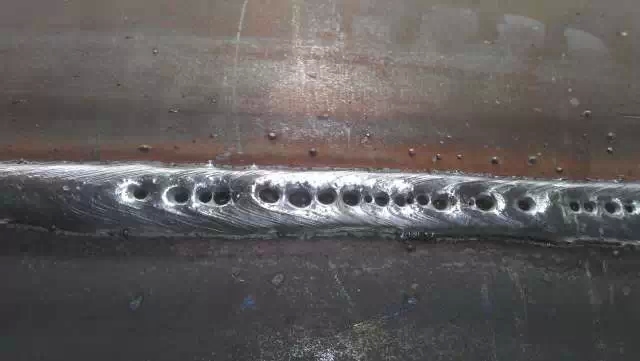
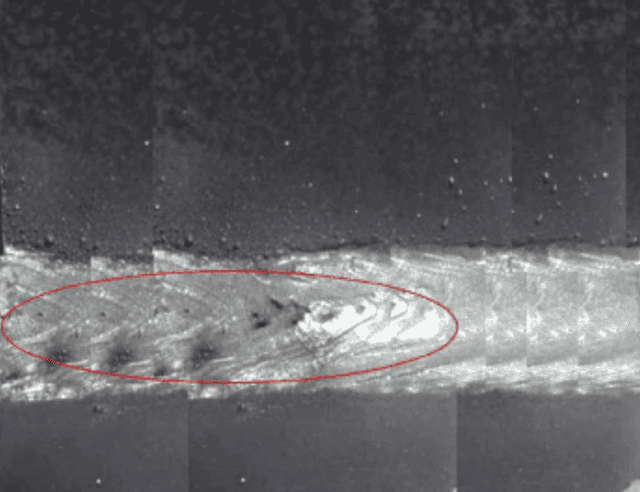
解决方法:对于气孔缺陷,其处理方法是铲去气孔处的焊缝金属,然后补焊;对于孔坑缩孔缺陷,其处理方法是在弧坑处补焊。
防治措施:
- 焊前仔细清理焊件坡口及坡口两侧的铁锈、油污、水份等,尽量减少氢的来源。
- 采用合理的保护气体流量;气流量L=焊丝直径∅×(10~15)L/min。
- 经常清理喷嘴。
- 控制焊丝伸出长度(导电嘴端部到工件的距离一般约等于焊丝直径的10~15倍且不超过25mm)
- 必要时,可进行预热,减少冷却速度。
- 控制焊接环境中风速的干扰。
咬边
咬边是指沿着焊趾,在母材部分形成的凹陷或者沟槽,它是由于电弧将焊缝边缘的母材熔化后没有得到熔敷金属的充分补充所留下的缺口。产生的原因一般有,电流太大、弧长太长、焊接速度过快、焊枪位置不当。
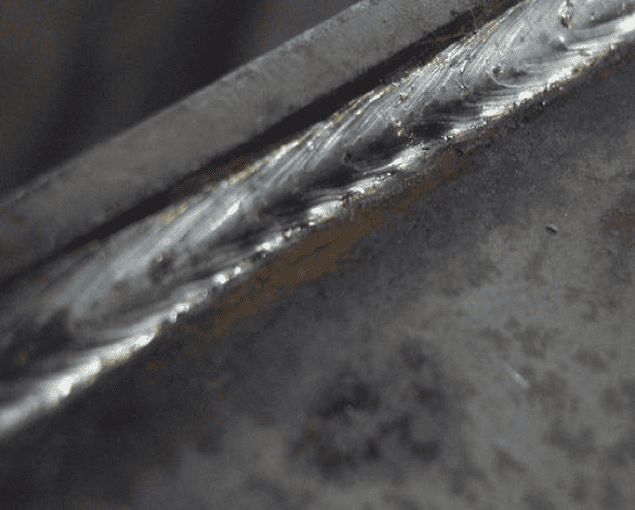
处理方法:轻微的、浅的咬边可用机械方法修锉,使其平滑过渡;严重的、深的咬边应进行焊补。
防治措施:
- 根据焊接工艺选择正确的焊接电流。
- 控制焊丝伸出长度不超过20mm。
- 角接焊时,焊枪和两个工件的夹角为45°(当两工件厚度不等时,焊丝对准的位置应偏向厚板,夹角为55°~80°);沿焊接方向,焊枪与垂直方向保持在10°~25°(前倾或后倾),焊丝对着两工件的夹角处或离夹角处1~2mm,匀速施焊。
未焊透
未焊透是指母材金属未熔化,焊缝金属没有进入接头根部的现象。产生原因主要有:焊接电流太小,熔深浅、间隙尺寸不合理、钝边太大。
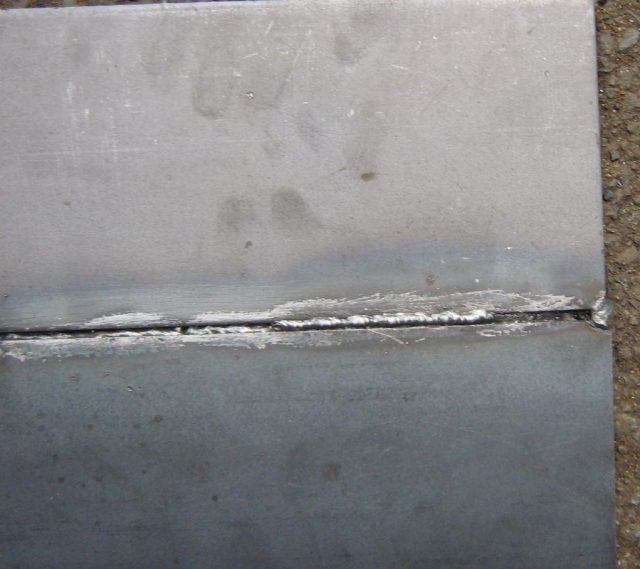
处理方法:对于敞开性好的结构的单面未焊透可在焊缝背面直接补焊。
防治措施:
- 根据钝边大小,选择合适的焊接电流。
- 设计合理的钝边尺寸。
未熔合
未熔合是指焊缝金属与母材金属,或焊缝金属之间未熔化结合在一起形成的缺陷。产生的原因主要有:焊接线能量太低、电弧指向偏斜(摆弧不恰当)、坡口侧壁有绣垢及污物、层间清渣不彻底等。
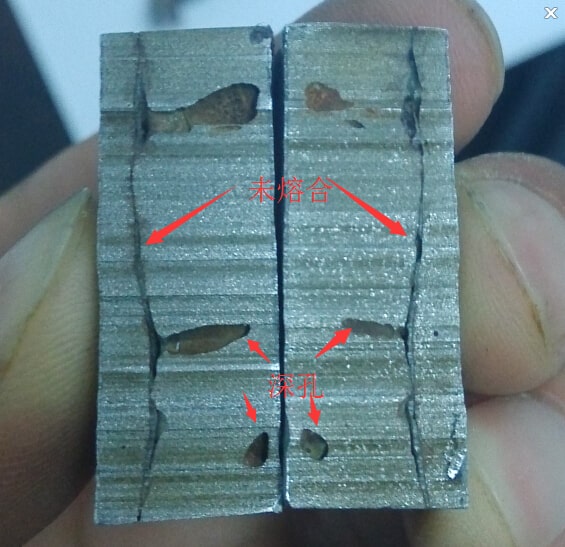
处理方法:对于未熔合应铲除未熔合处的焊缝金属后补焊。
防治措施:
- 正确选用线能量(按焊接工艺规范要求选择)。
- 调整焊枪角度。一般焊枪与角接的两工件成45º,当两工件不等厚时,焊丝指向稍微偏向厚板的一边。对接打底时,焊丝需对准焊缝根部。
- 认真操作,加强坡口两侧和层间清理等。
固体夹杂
有夹渣和夹钨两种缺陷。产生夹渣的主要原因是焊接材料质量不好、焊接电流太小、焊接速度太快、熔渣密度太大、阻碍熔渣上浮、多层焊时熔渣未清除干净等。产生夹钨的主要原因是氩弧焊时钨极与熔池金属接触。
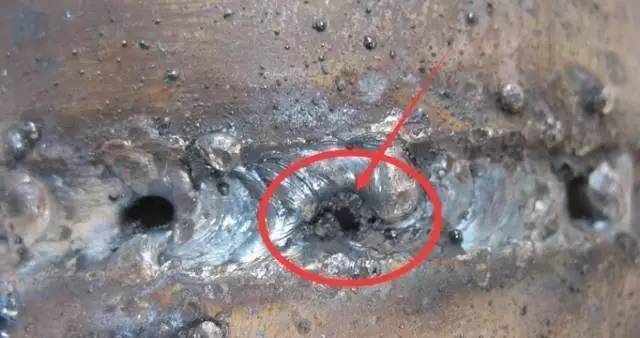
处理方法:对于夹渣的缺陷,其处理方法是铲除夹渣处的焊缝金属,然后焊补。对于夹钨的缺陷,其处理方法是挖去夹钨处缺陷金属,重新焊补。
防治措施:
- 正确选择焊接参数,让熔渣能够浮出熔池。
- 正确、有规则的运弧,搅拌熔池,使铁水与熔渣分离。
- 及时清除各层焊渣及飞溅。
焊瘤
焊瘤是指焊接过程中金属流溢到加热不足的母材或者焊缝上,未能和母材或者前道焊缝熔合在一起而堆积的金属缺陷。产生的主要原因有:焊接电流及电压太大、焊接速度太慢、装配间隙太大。
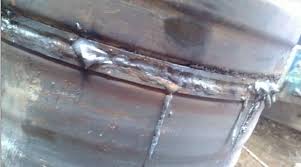
处理方法:用铲、锉、磨等手工或机械方法除去多余的堆积金属。
防治措施:
- 正确选用焊接工艺参数,提高操作技能的熟练程度。
- 严格控制装配间隙。
烧穿
烧穿是指焊接过程中熔敷金属自坡口背面流出,形成穿孔的缺陷。产生的原因主要有:焊接电流过大、焊接速度太慢、装配间隙太大。
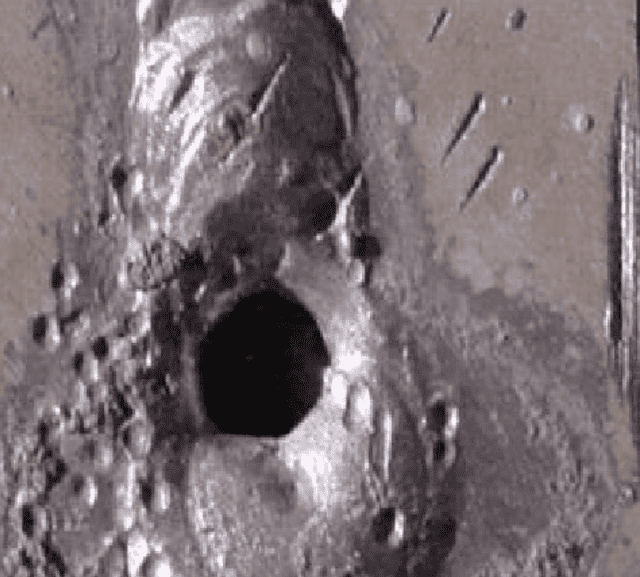
处理方法:穿后要立即停止焊接,需打磨出坡口角度和根部间隙,再重新进行根焊、热焊至完成本道工序。
防治措施:
- 选择合适的焊接电流和焊接速度。
- 严格控制装配间隙。
飞溅
飞溅是指熔化的金属飞向熔池之外,粘接在母材或者焊道表面上形成的单个或者成簇的金属颗粒。产生的原因主要有:焊接工艺参数选择不当,即焊接电流与电压不匹配、焊枪倾角过大。
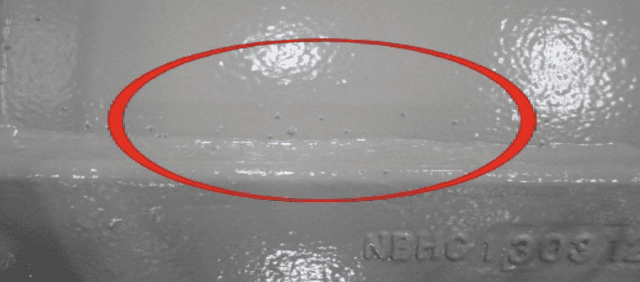
处理方法:对焊缝及其两侧母材表面产生一般性飞溅时,可用锉刀或手铲等工具除掉即可,如果属于熔合性飞溅时,可用砂轮打磨法彻底除掉,与焊缝母材相平(打磨深度不得超过0.5毫米)。
防治措施:
- 正确的选用焊接工艺参数。
- 焊丝伸出长度不超过25mm,以刚好可以看清熔池为宜。
- 焊枪的倾角保持在10º~25º之间。
射线探伤(RT探伤)图谱
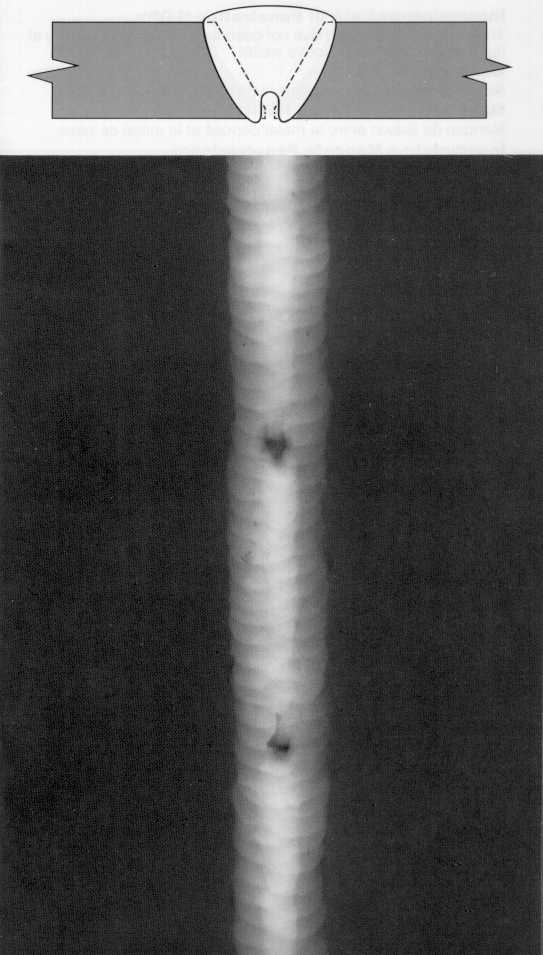
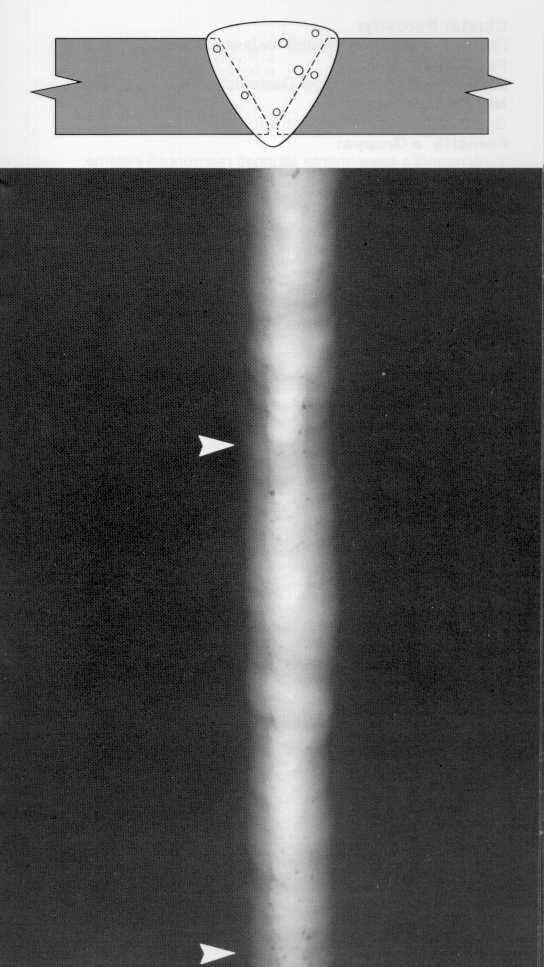
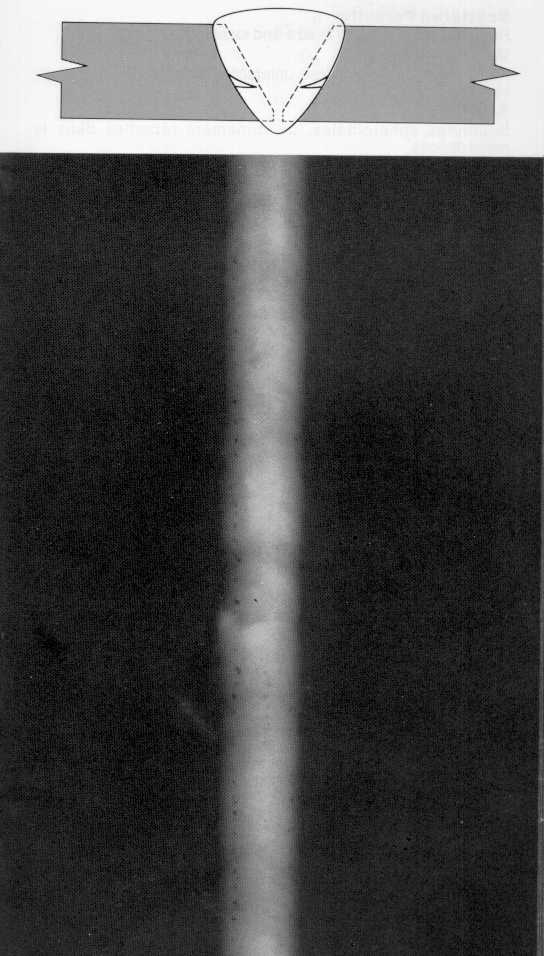
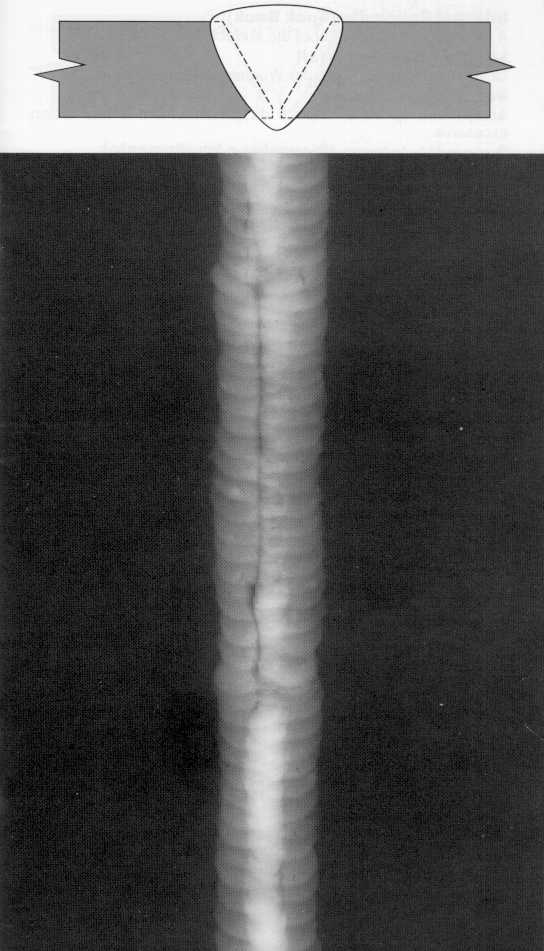
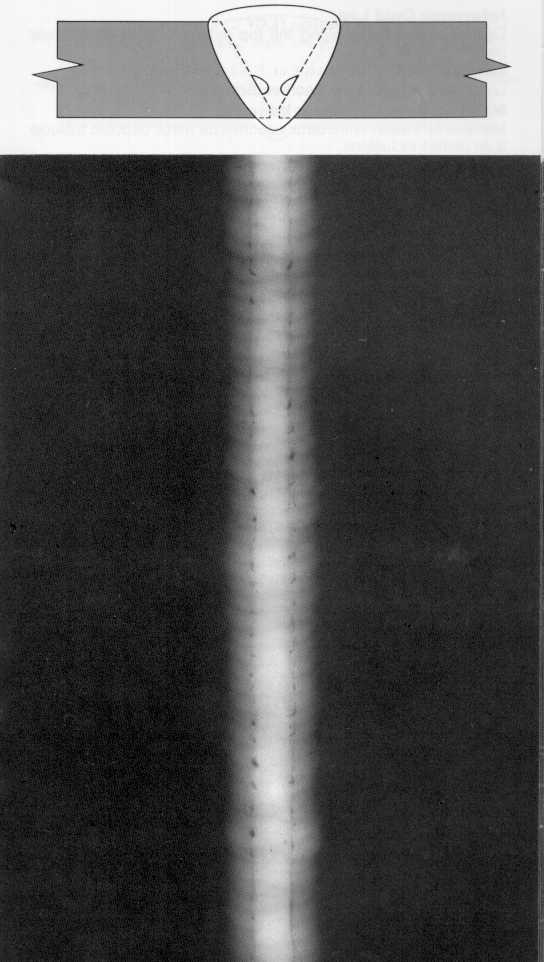
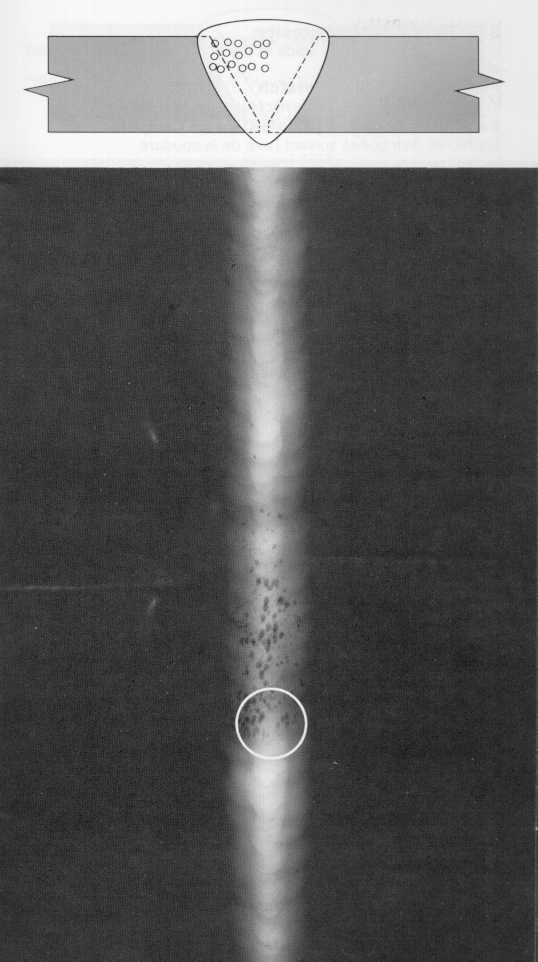
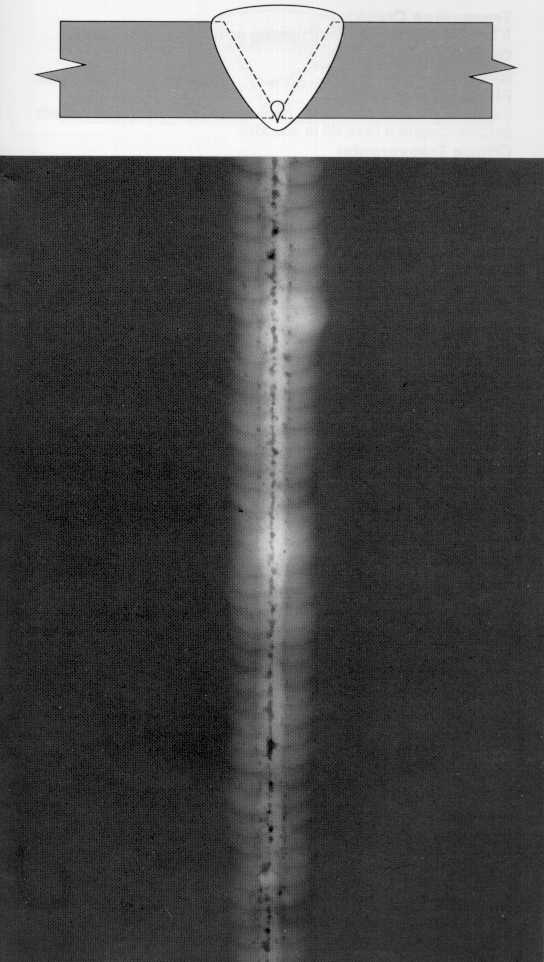
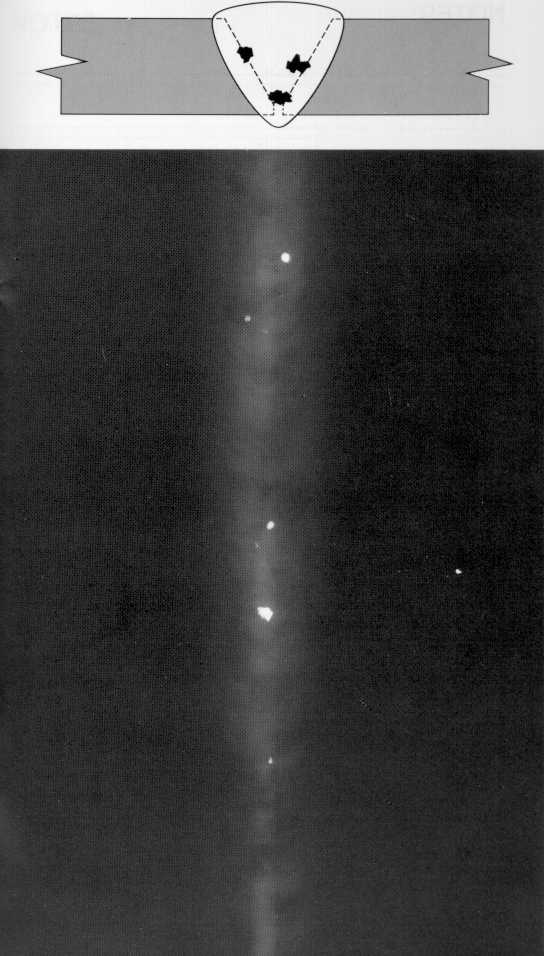
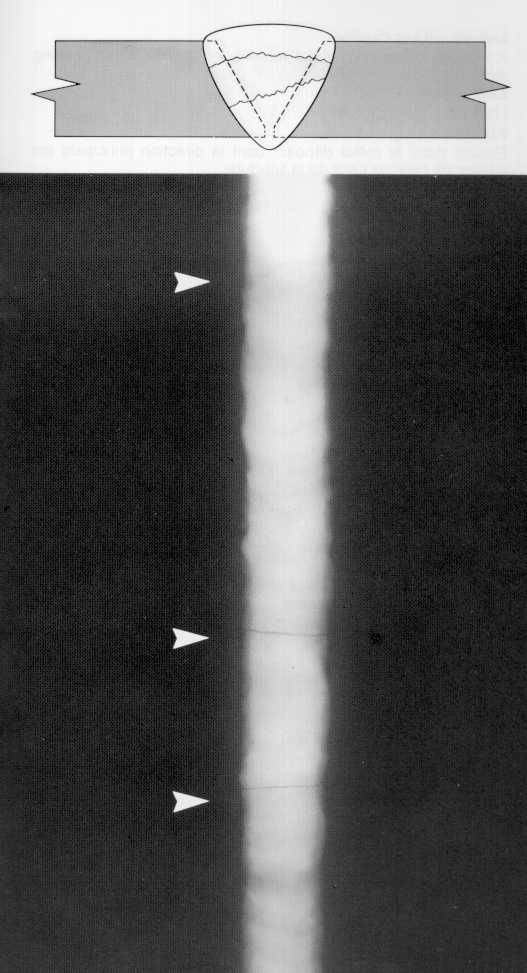
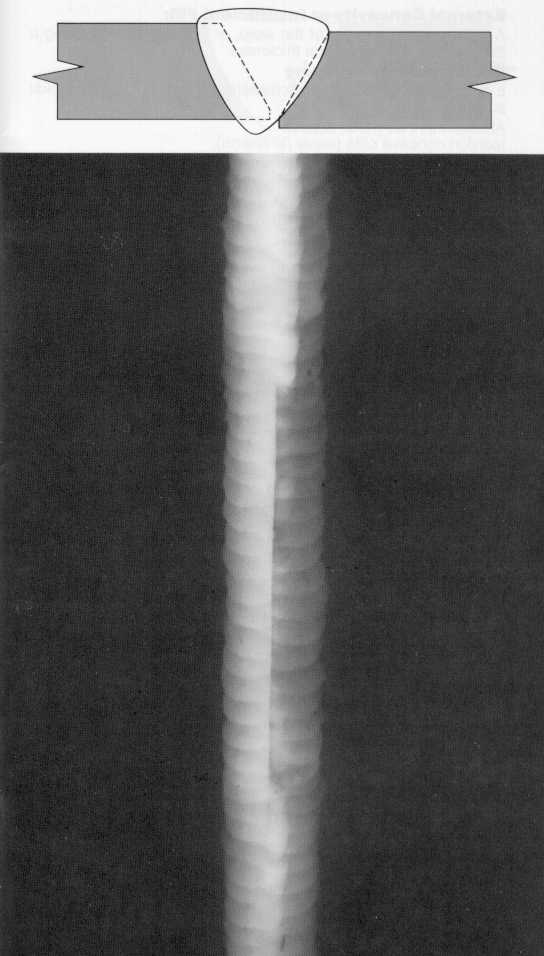
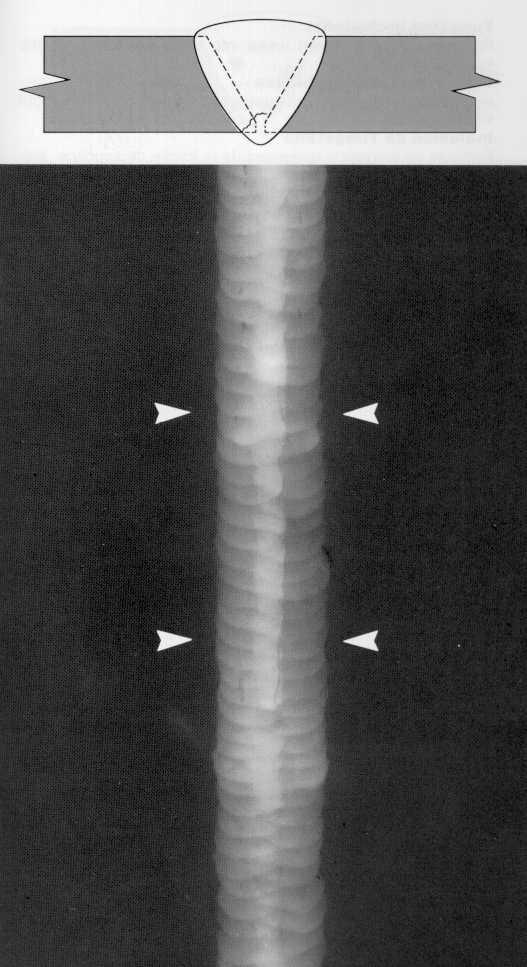
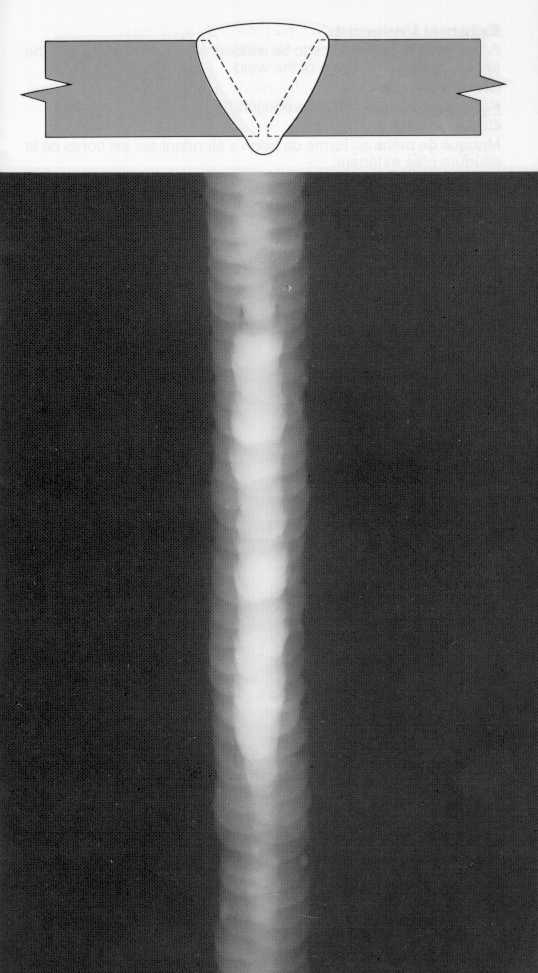
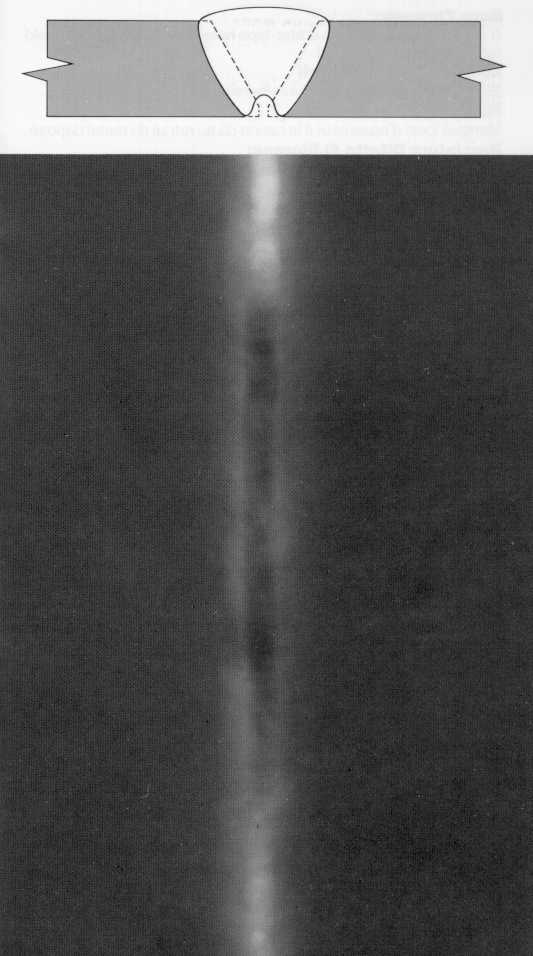
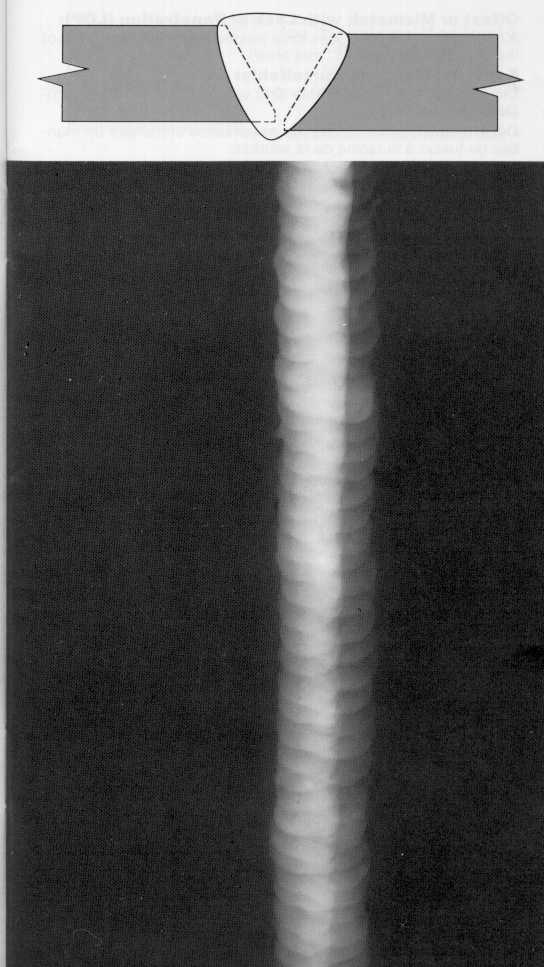
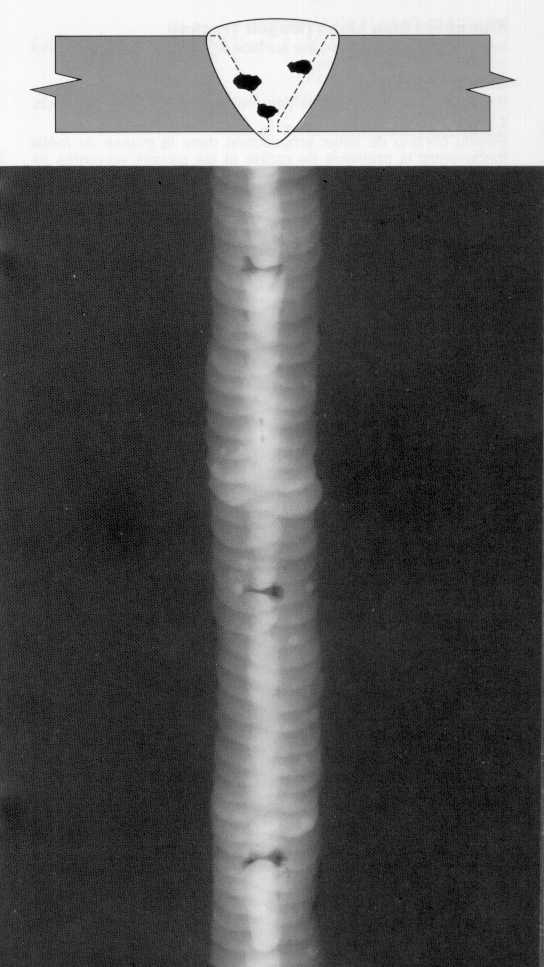